-
-
Notifications
You must be signed in to change notification settings - Fork 18
New issue
Have a question about this project? Sign up for a free GitHub account to open an issue and contact its maintainers and the community.
By clicking “Sign up for GitHub”, you agree to our terms of service and privacy statement. We’ll occasionally send you account related emails.
Already on GitHub? Sign in to your account
3D milling incomplete curves, Rhino 5 #68
Comments
Hi. Thank you so much for your feedback! The rhino/gh offset function is not so robust unfortunately, and sometimes give buggy results that we dont handle so well with gh list management. I am on holiday now and have laptop break in order to heal some RSI in my wrist, so I cannot have look at your file now. I will get back to you in a few weeks. In the meantime i recommend you to set up individual pocket jobs for better control. You can also put flat single surfaces in the 3D layer and get automatic pocket depth. You can also manually edit the areas to be pocketed so no gap is too narrow for the milling bit to pass, giving you one continuous pocket from a surface or curves. When you put geometry in the 3D layer you get an automatic cutout job next to pocket and 3D rroughing and finishing. You can disable the cutout job in the advanced 3D settings panel if you want. |
I'm on holidays myself as well but will have a look as soon as I'm back! |
As a followup I fixed some of the problems by doing an offset to the original object before generating g-code. Rhino 5 again. I have looked at using the inside cutting to create molds. Using a simple square/rectangle solid set -z it seems as though the cutting is below the bottom of the object. Can anyone verify if this happens in Rhino 6 version? <<CNC 3d layer >> Please. Thanks. |
Is this the same as the previous file you uploaded here or did you forget to upload a new file? |
Hi Siemen, I just saw this email. I did not up load a file. I created a solid 10x40x-10(x,y,z) at the origin. I used the rhino archive version 5 Bark Beetle, parameter changes>>>>>
Pass depth factor to 0.2.Material to wax.Object on the CNC 3D layerInside cutting YES
I get three passes first at approx. z = -3.5, second z= -7.0, third z=-10.5.
Thank You Again and Again. Al Mowery
On Monday, November 2, 2020, 3:52:02 AM CST, Siemen Cuypers <[email protected]> wrote:
Is this the same as the previous file you uploaded here or did you forget to upload a new file?
—
You are receiving this because you authored the thread.
Reply to this email directly, view it on GitHub, or unsubscribe.
|
Here is the Rhino 5 file. Thanks AL
On Sunday, November 8, 2020, 6:32:35 PM CST, Alfred Mowery <[email protected]> wrote:
Hi Siemen, I just saw this email. I did not up load a file. I created a solid 10x40x-10(x,y,z) at the origin. I used the rhino archive version 5 Bark Beetle, parameter changes>>>>>
Pass depth factor to 0.2.Material to wax.Object on the CNC 3D layerInside cutting YES
I get three passes first at approx. z = -3.5, second z= -7.0, third z=-10.5.
Thank You Again and Again. Al Mowery
On Monday, November 2, 2020, 3:52:02 AM CST, Siemen Cuypers <[email protected]> wrote:
Is this the same as the previous file you uploaded here or did you forget to upload a new file?
—
You are receiving this because you authored the thread.
Reply to this email directly, view it on GitHub, or unsubscribe.
|
I have been using pockets extensively, couple fixes for rounding. But overall great software. 3D milling many problems. Could someone check on rhino 6? Thanks. I would like to help fix bugs if i am pointed to some direction. I have to modify the bit size to go down to .5mm for my wax cutting. The pic shows pocket(edge cutting) on left object does not go all the way down. The middle object the milling goes below the object, both pocket and milling. Ready to move to rhino 6, BB version 5 is just hopefully buggy and version 6 is better. Thanks.
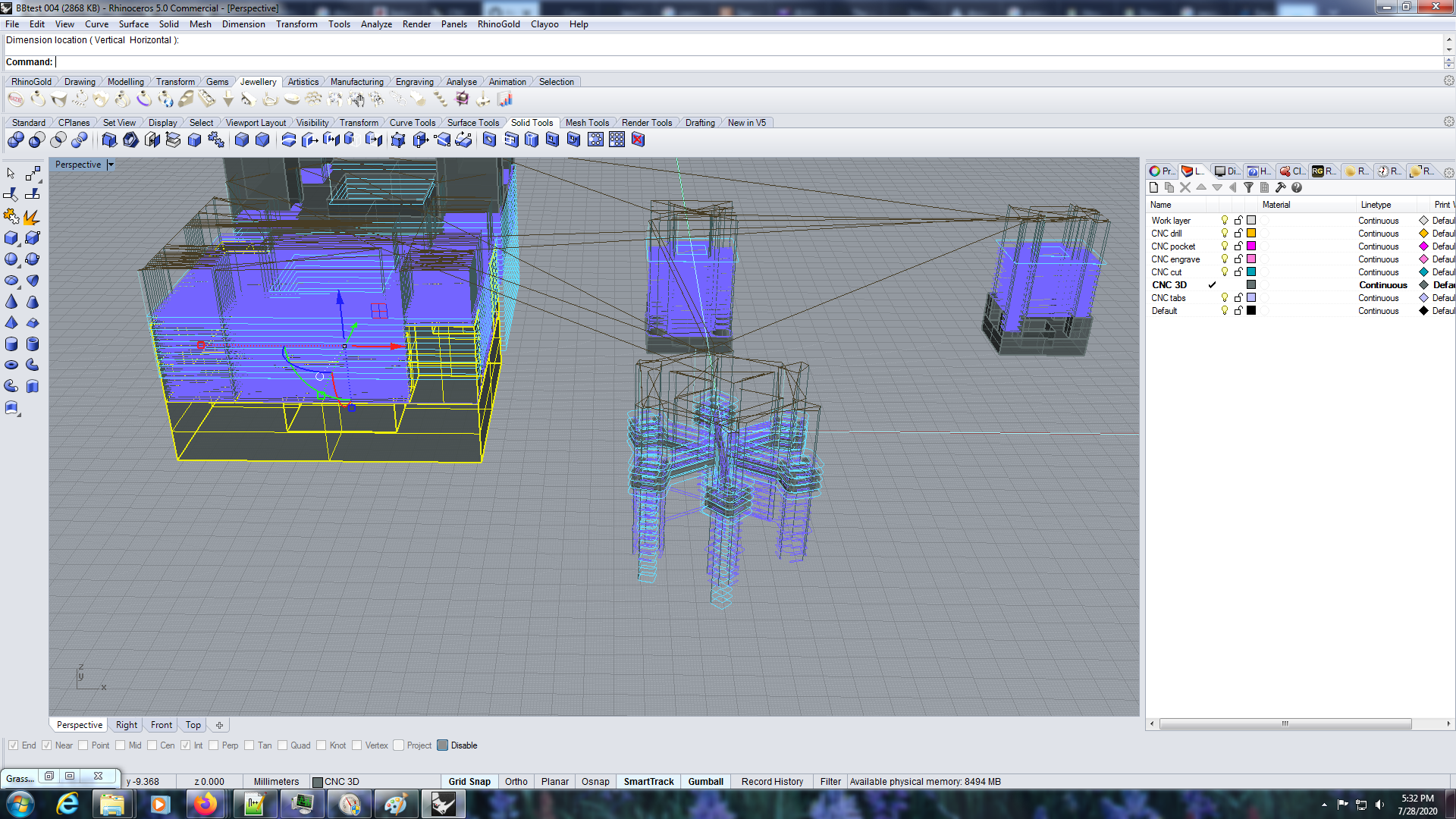
BBtest 004.zip
The text was updated successfully, but these errors were encountered: